Lithium has become, in a few years, a highly demanded mineral, driven mainly by the increase in the electric car industry. But among the critics are those who indicate that traditional extraction is harmful to the environment and a significant source of polluting emissions. Now, the industry moves towards a much more sustainable and economical way to extract what is beginning to be called “green lithium.”
The point is that demand is growing so much that, according to the World Bank, it will be necessary to multiply the current production by five to meet the objectives of implementing electric mobility for 2050. Something that will mean the opening of new fields.
Currently, lithium is obtained mainly from hard rock mines, such as those in Australia, or underground brine deposits located under the surface of dry lakes, mostly in Chile and Argentina. This type of hard rock mining, where the mineral is extracted from open-pit mines and then dried using many fossil fuels, impacts the landscape and requires a large amount of water in places where the supply is usually deficient. It is estimated that it releases about 15 tons of CO2 for every ton of lithium produced.
The other conventional option, mining lithium from underground deposits, relies on even more water to extract lithium and takes place in parts of the world that are often water-scarce, a concern for local communities.
The alternative: geothermal waters
Lithium extraction from geothermal waters is spreading as a much more sustainable form of production. This is found in different research projects in other markets, both in Europe, with ongoing projects in places like Germany or the United Kingdom, and in the United States. A format that is characterized by having a much smaller environmental footprint compared to the current format.
Geothermal brine is a hot, concentrated saline solution circulated through very hot rocks and has been enriched with lithium, boron, and potassium. The energy-consuming process of extracting lithium from the solid rock is powered by natural geothermal energy.
One of the projects investigating the potential of this format is located in the British town of Cornwall. The copper mines opened more than 100 years ago showed enormous lithium concentrations in the water, between eight and ten times more than usual. But at that time, the demand for lithium was not significant. Now, scientists have returned to this site to develop a system that allows the efficient extraction of this precious mineral.
According to early studies, the brine in Cornish mines has concentrations of up to 260 milligrams per liter, flowing at a rate of between 40 and 60 liters per second. Enough to produce lithium to power a mobile phone battery in seconds.
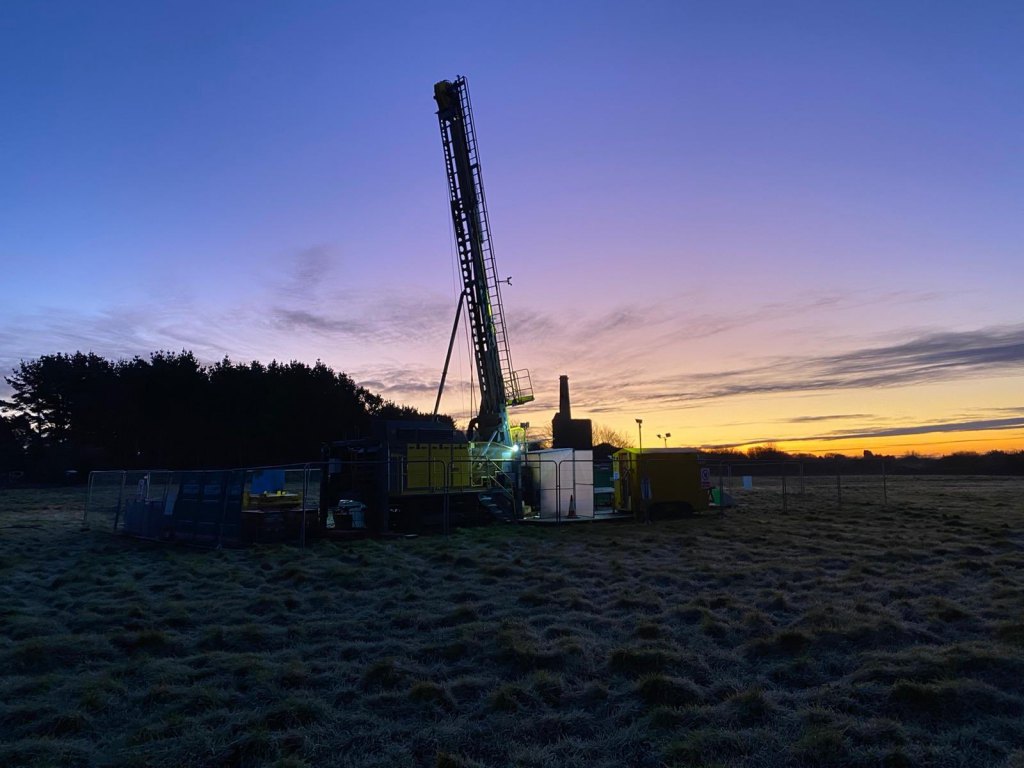
Compared to other traditional methods of lithium production, the process has several advantages: it takes advantage of the existing infrastructure of geothermal plants, it is not necessary to alter the terrain, the thermal waters are returned to the ground after use, no harmful substances are released, and the production of heat and electricity in geothermal plants is not altered.
But this is not the only format, and other sustainable lithium extraction alternatives are being studied in other parts of the world. In the United States, William Stringfellow, director of the Ecological Engineering Research Program at Lawrence Berkeley National Laboratory, researches the United States Department of Energy on different extracting lithium methods from brine.
One approach is to extract lithium from brines using solvents designed to collect lithium ions. In contrast, others include membranes that only allow lithium ions to pass through and electrochemical separation, where lithium ions are attracted to charged electrodes.
According to those responsible for this project, all methods have one main obstacle: obtaining only lithium from water. According to William Stringfellow: “There are many other materials in the brine that potentially interfere with the lithium extraction process [such as sodium and magnesium], so you must control and remove them.”
In Germany, they are also working on a simulation project. Located in the Rhine Valley, lithium and geothermal energy developer Vulcan Energy Resources works to pump hot geothermal brine to the surface and use the heat to power its lithium extraction process and return the excess to the grid.