The search for a miracle battery that boosts energy density and reduces costs has become one of the main trends in the industrial sector. One of the technologies with the greatest potential for the future is solid electrolyte, and one of the companies that are betting the most on this concept is Toyota, which this week has given an update on the status of its work.
Keiji Kaita, executive vice president of Toyota’s engine division, has stated in statements to the Autonews portal that they already have a functional prototype of this promising type of batteries, but that they still have to work to solve some of the main problems that slow their arrival on the market.
These are mainly focused on their useful life. According to the Japanese executive, the biggest problem they encounter is that the batteries fail after several charging cycles in a row—a challenge for the brand that is looking for a solution.
From Toyota, it has been indicated that they work on the formula that allows them to overcome the substantial electrolyte problems, such as adjusting the anode or other materials that shape it. One of them is to use a combination of sulfur, which allows it to improve the transfer between the electrodes. In addition to a longer useful life, it would enable the development of batteries with a high energy density and a low cost when using abundant materials.
The challenge for Toyota and Panasonic is to develop an electrolyte that does not deform during the charge and discharge processes and thereby achieve an efficient and durable system.
A solid electrolyte technology where the Korean Samsung also works, which has chosen a different approach by not replacing the electrolyte, but the lithium anode that has been replaced by a silver-carbon compound that allows reducing the degradation of the electrolyte during the loading processes.
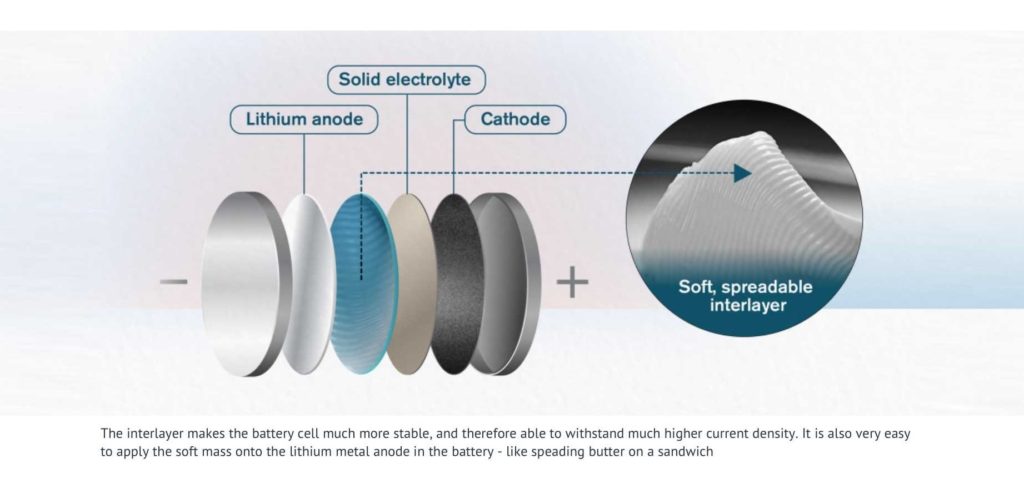
Another challenge that this technology faces is its difficult industrial escalation. Ultra dry environments are required for production, which currently means that the work is carried out in small cabins where operators use integrated gloves to complete their work. Something that translates into the need to develop expensive facilities for mass production once the technical challenges have been overcome.
Despite everything, from Toyota, they hope to have the technology ready for production in 2025. An alternative with a high energy density, a tolerance to ultra-fast recharges, and a high level of safety, but which will be weighed down in the first phase by a high price, will make you lose competitiveness with the current batteries